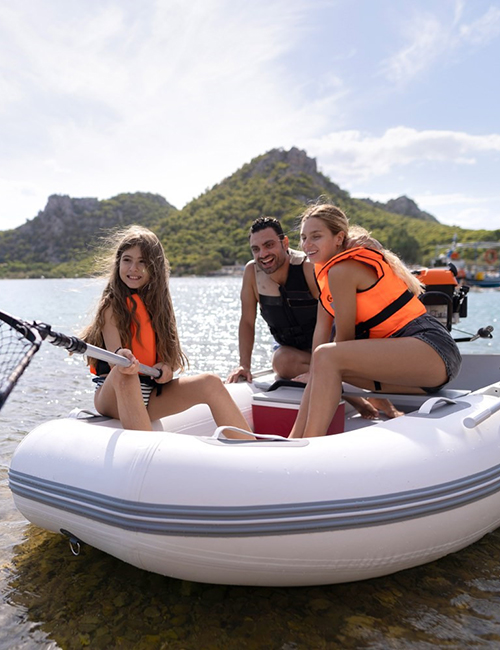
Welding vs. Gluing
What makes the glue let go?
Plasticizer migration is what is responsible for adhesive bonds losing their strength over time. The plasticizer is the same thing in the coating that keeps the UV radiation from destroying your boat. This is one reason why PVC boats last so long under UV, but also the reason why the glue can let go after a number of years. This migration process is accelerated with heat and Humidity. So a glued boat left in a closet near the beach in the tropics may lose it’s glued parts in 1 year, Over our production experience, we replace a lot of glued parts and even tried different brands of adhesive, and we see all kinds of conditions boats are exposed to. Glue failure happens on Hypalon boats as well, it just takes a little longer.
The Welding Process
Hot air welding uses hot air to heat the coating on the fabric where it is to be bonded together. A Nozzle is situated between two rollers that pull the material through the machine. As the material is pulled through the machine, hot air is applied to the surfaces to be fused together. Pressure from the rollers and heat form the hot air cause the plastic to fuse as the plastic cools. With the material moving through a machine like this, different shapes can be made. Patterns can then be put together to form the shape of an inflatable boat. Colton yacht’s unique welding process techniques allow us to join sectional seams and longitudinal ones. It significantly expands the possibilities of our designers while creating new models and allows a higher degree of optimization of vessel shapes and an increase in navigability and safety of the boat. Additionally, this technology makes the seams elastic and solid, making the structure of your dinghy almost stable when fully inflated. Our welders own at least 5 years experience and could control good quality for every detail.
The Gluing Process
When gluing plastic coated boat fabrics there are three steps involved:
the boat fabric must be carefully prepared
the glue must be applied
the pieces must be assembled and bonded together
The quality of the seam is dependent on a number of factors:
how hard the material is to prepare
how carefully the material is prepared
how carefully the glue is applied
environmental factors like humidity effect the glue bond
Gluing processes consist of preparation, application and bonding of the fabrics together. The quality of a glued joint is determined by how hard the material is to prepare, how well it is prepared, and environmental factors that may affect the adhesive. Parts can be stockpiled at many different stages of production. I believe that this is how efficiency is obtained in this process.
Pros and Cons
Glue
· Pro: Glued seams are more flexible over time and can have higher holding power in complex shapes.
· Pro: Glue boats are easily to be repaired.
· Pro: Glue gets ruined over time with heat and humidity, causing leaks to be repairs.
· Con: Gluing seems to be a complex process that requires special conditions and, if something goes wrong - leads to a failure of the seam shortly.
· Con: Glue produces chemicals harmful to the environment, such as air and water.
Heat welding
· Pro: The Boats feature a high level of toughness due to how seams bond together, creating strength. These boats can be used in colder waters, and they don't show any signs of wear.
· Pro: Heat-welded seams are more consistent and don't require a particular environment to be created, as the heat welding process uses only high temperatures.
· Pro: Safe for the environment
· Con: Welded seams are also not 100% repairable, they can only be patched over.
· Con: Welding boat has high requirement for workers’ skilled technology. If welded not in proper way. Boat will be easily leaking.